Reliable Safety and Leakage Detection for Challenging Environments
Early leak detection is vital to ensure safety and provide early warnings to avoid damage. HB Products offers a range of sensors designed to detect and protect your refrigeration system, stored goods, and employees. With Gas Alarms, pH Sensors, Compressor protection sensors, and Cascade Systems, you can find a solution to safeguard against liquid slugging, compressor damage, clogged systems, and costly repairs.
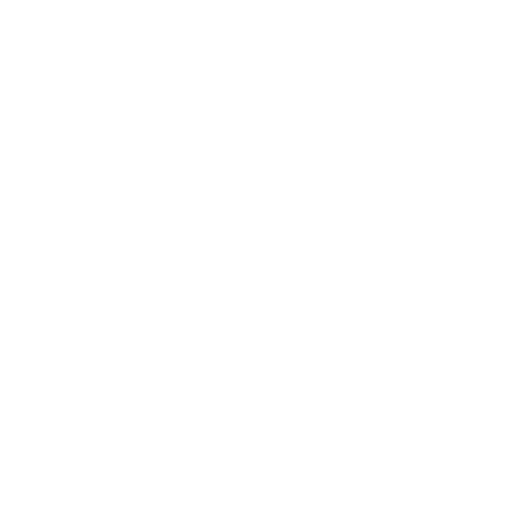
Achieve Safety and Compliance with Our Gas Detection Alarms
Our Gas Alarms are designed to detect small amounts of leaking refrigerant in areas such as cold storage facilities and machine rooms in order to provide early warning and avoid harm.
Our Gas Alarms come in different variations for both CO2 and ammonia that fulfill the requirements for gas leakage measurement in accordance with F-GAS regulation EU/517/2014.
The Gas Alarms provide easy integration as they can be configured with HB Tool. To further enhance safety, we offer a service kit to assist you with the maintenance.
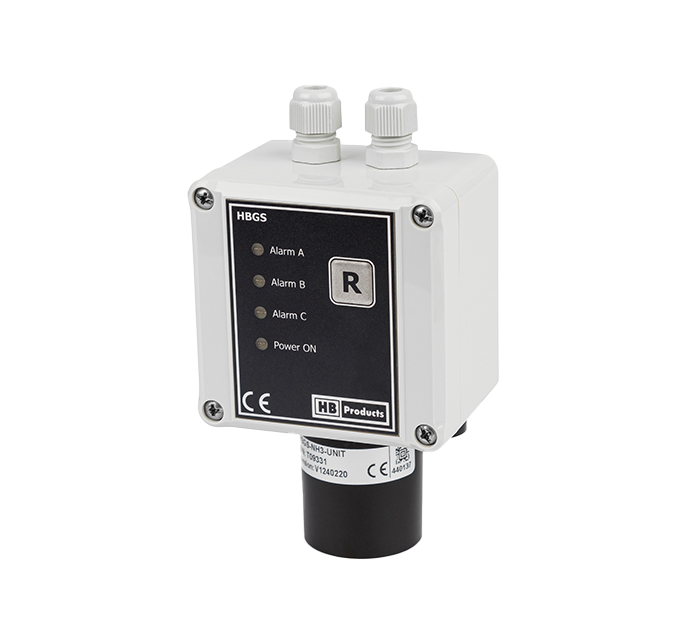
Easy Brine Leakage Detection With a pH Sensor
Our pH Sensors are highly sensitive and designed to detect ammonia levels above 100 ppm in water and glycol brines.
To enhance durability, the pH Sensors have a protected universal flat-faced glass process electrode specially designed for tough applications.
Additionally, the pH Sensors have a “semi-flush” design to minimize the build-up of dirt on the probe and to ensure easy maintenance and low costs.
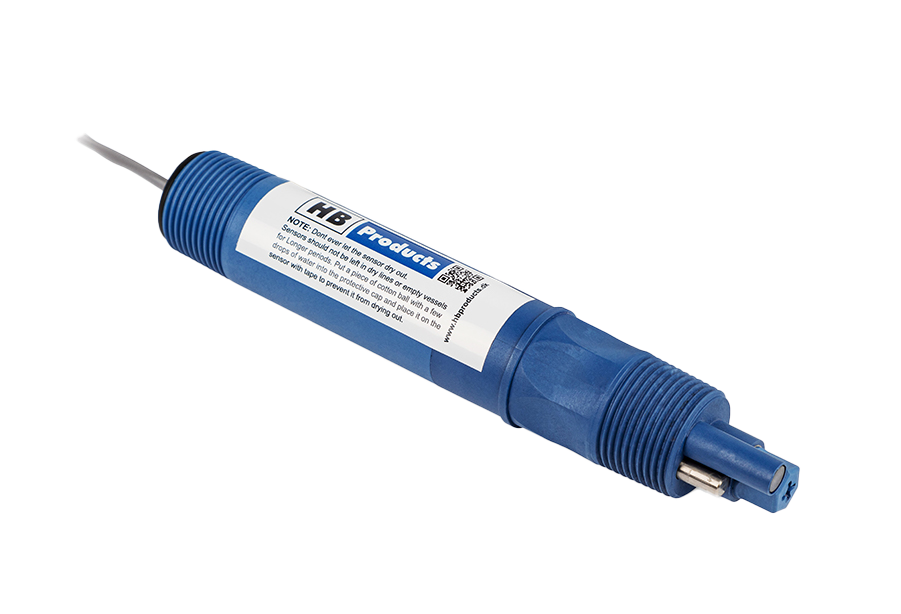
Download Our Brochures If You Are Interested in Learning More About Our Safety and Leakage Detection
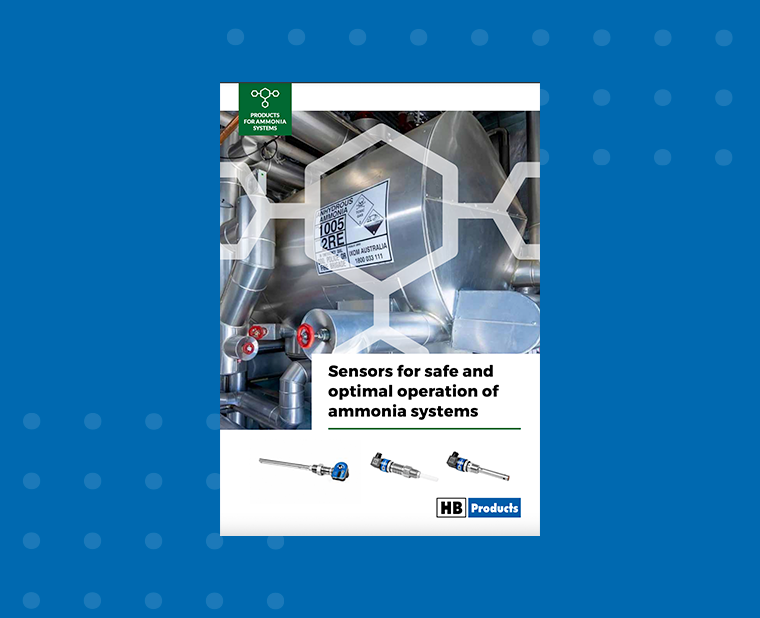
HB Products solutions for safe operations of ammonia systems
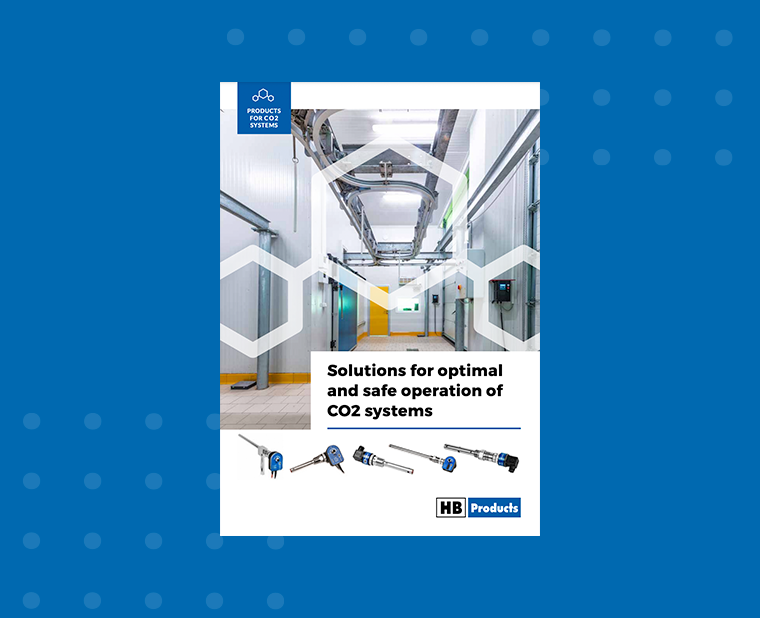
HB Products solutions for safe operations of CO2 systems
Prevent Damage to Compressors With Compressor Protection
Our Compressor Protection Sensors monitor the suction line in front of the compressor, providing an alert when liquids are detected, thereby safeguarding functionality and helping to prevent damage to the system.
We offer two versions: the Strainer Housing and the Rod Style.
The Rod Style Sensor must be installed in an elbow at the end of a horizontal pipe, at the bottom, where the liquid flows. The Strainer Housing Sensor is installed in an empty strainer housing and measures all the liquid flowing along the walls.
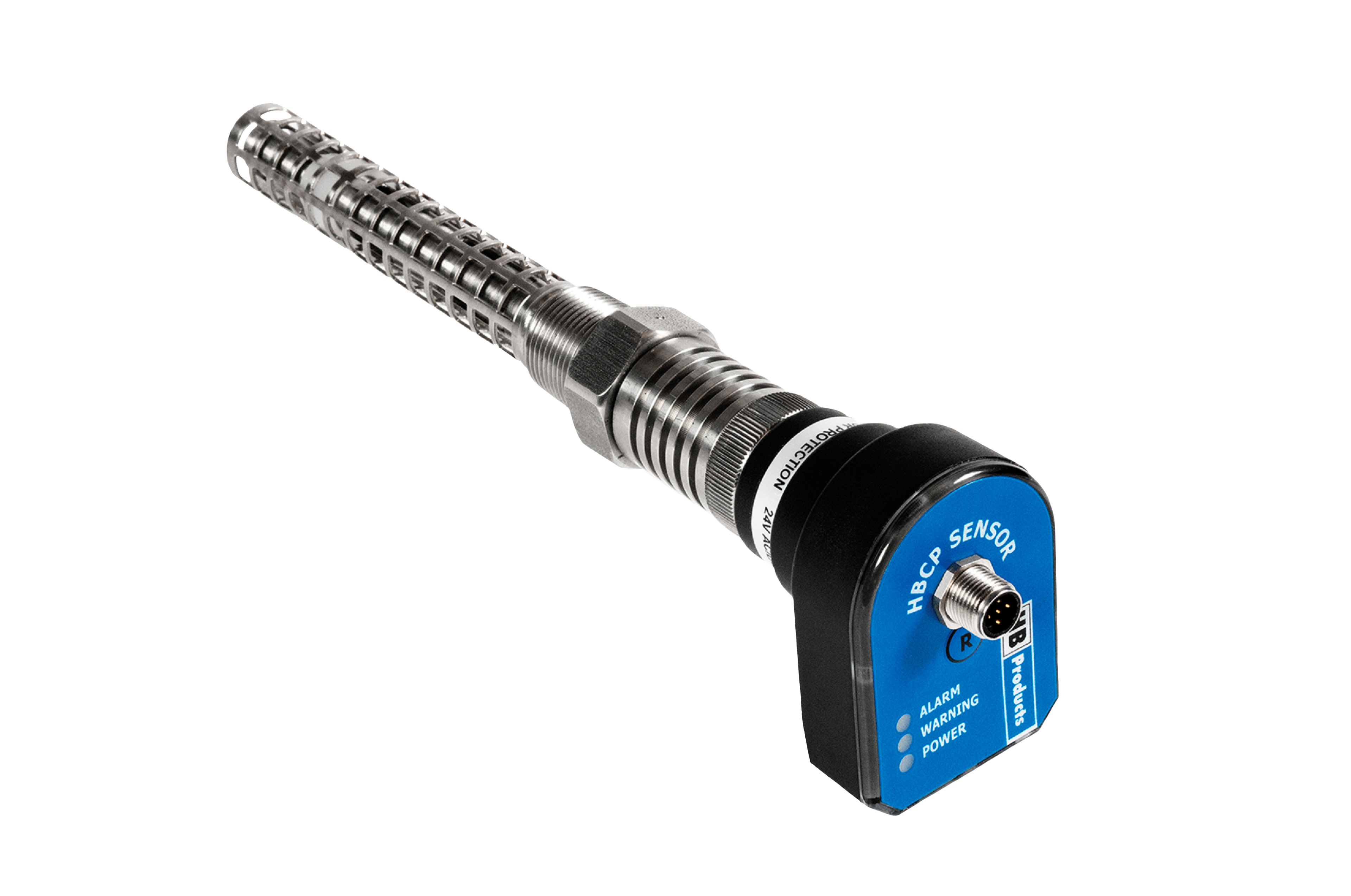
Cascade Leakage Detection in Liquid Ammonia
Cascade systems that use CO2 and ammonia face challenges with the leakage of CO2 into ammonia, and failure to address it promptly can cause significant downtime and damage to the entire ammonia system.
Our sensors are designed to detect and resolve such issues, ensuring the safety and longevity of refrigeration systems by triggering a digital alarm and increasing mA output when ammonium carbamate is detected in the ammonia.
For optimal detection, install the sensor at the bottom of the vessel. However, it can be installed in any position as long as it is covered by liquid ammonia.
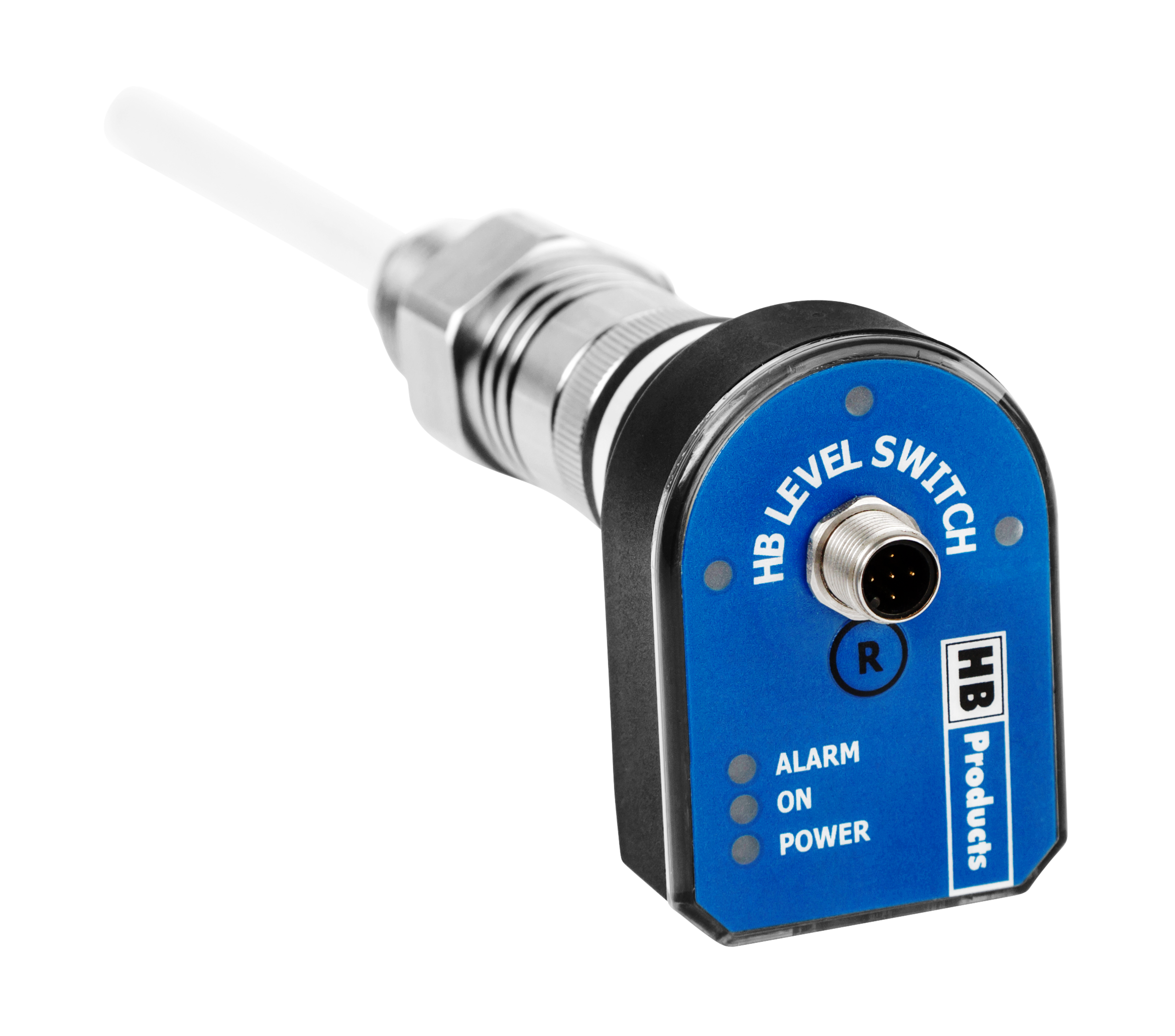
You Might Also Be Interested in Looking at Our Other Products
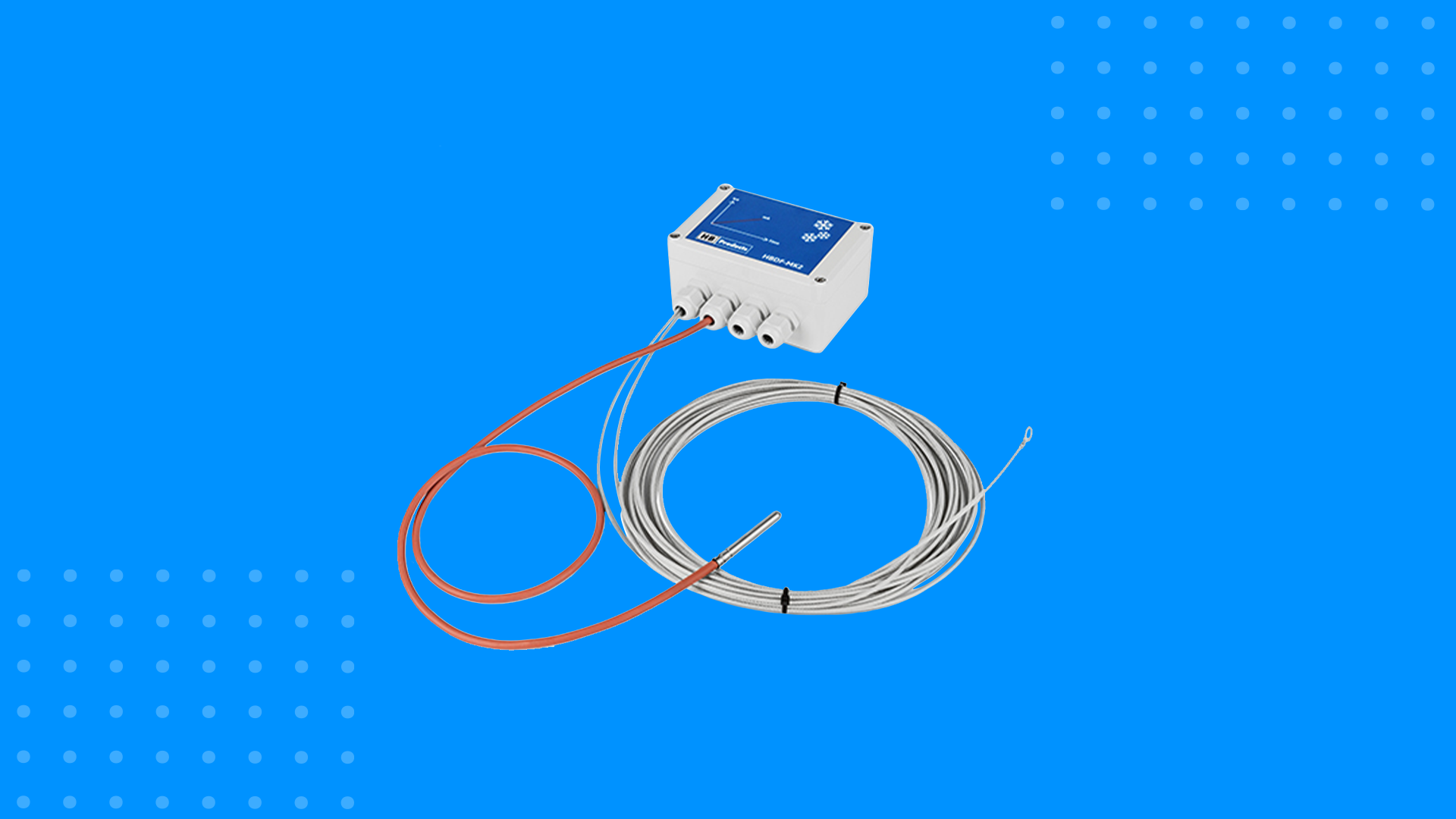
Optimize Your Defrost Cycles with Our Defrost Sensor
By measuring frost accumulation on the surface, our Defrost Sensor initiates defrost cycles only when necessary. This prevents excessive buildup while saving time, money, and energy in the process.
Learn more about the Defrost Sensor by clicking the link below.
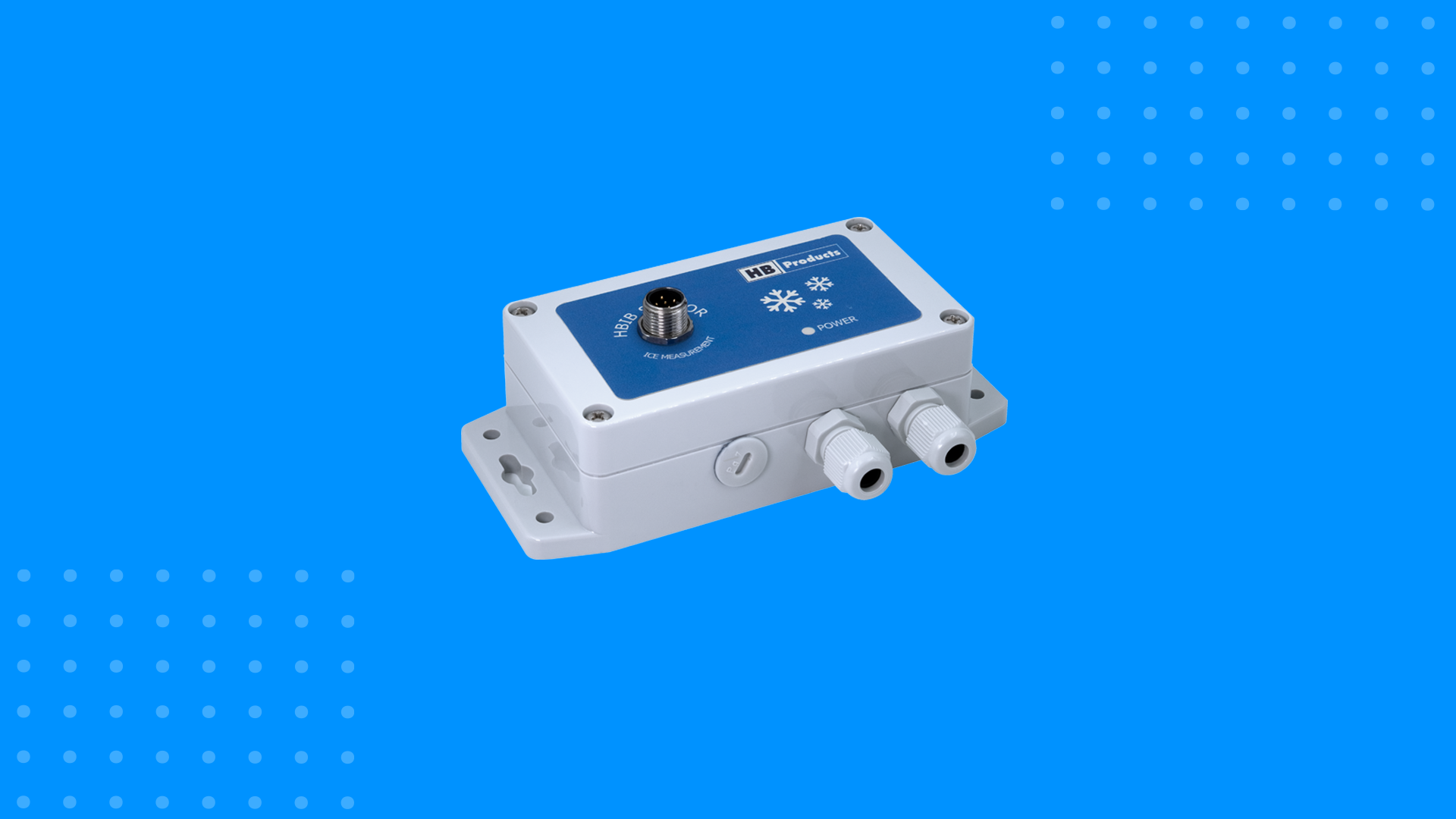
Measure and Maintain Ice Thickness with Our Ice Bank Sensor
Our Ice Bank Sensor is designed to provide greater control over your refrigeration system by maintaining optimal ice thickness and utilizing off-peak hours for a more cost-effective solution.
Learn more about the Ice Bank Sensor by clicking the link below.
Avoid Excessive Defrost Cycles Without Compromising on Performance and Cooling Capacity
The Defrost Sensor can be installed on both new and existing systems and has shown a reduction in the number of defrost cycles, which typically accumulates to a 20-40% savings in energy costs.
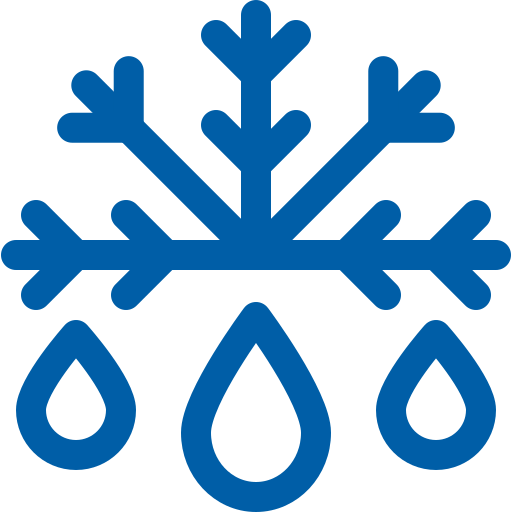
Reduce defrost cycles by up to 50-70%
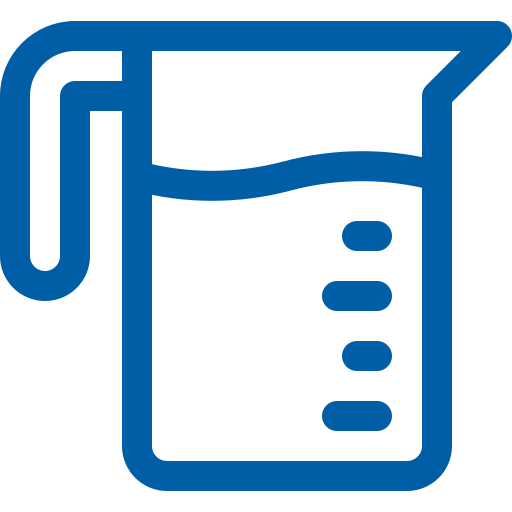
Based on the capacitive measuring principle
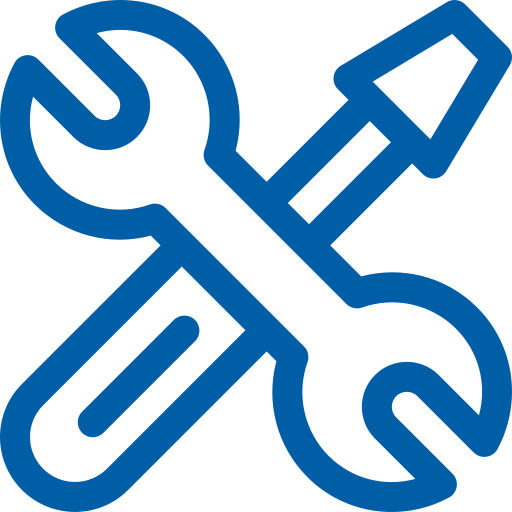
Easy installation without system shutdown
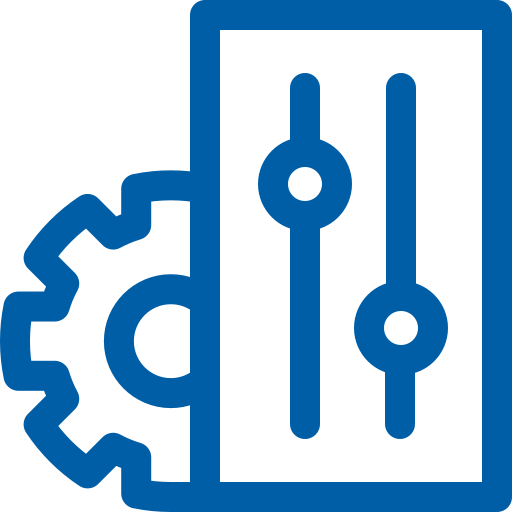
Options to choose between control modes for convenient control
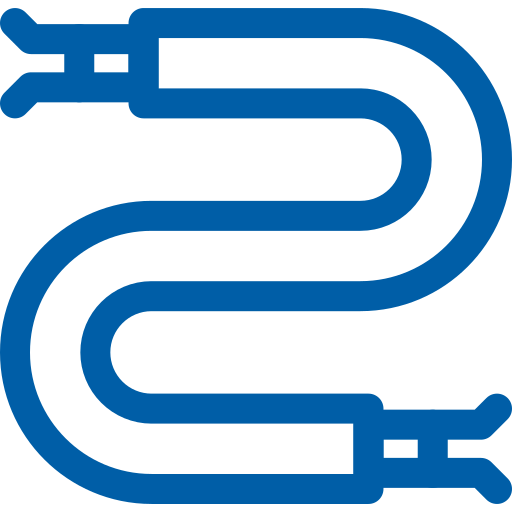
Available in 4 versions with wire lengths ranging from 10 to 30 meters
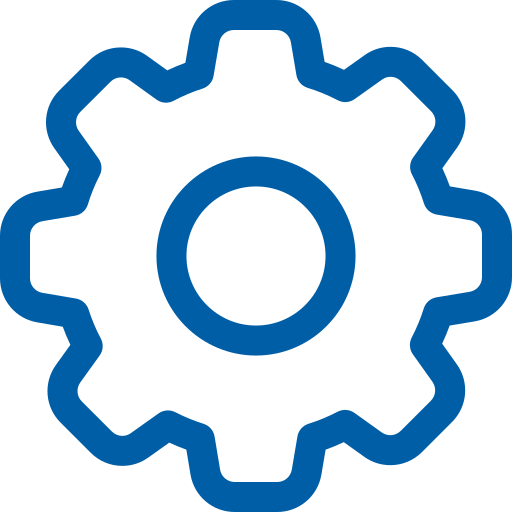
Accurate configuration with HB Tool
Learn How the Defrost Sensor Works
How to Reduce the Energy-Consumption and Save Money in Your Cold Storage Facility
Would you like to learn more about the benefits of installing our Defrost Sensor on your new or existing evaporators? Download our brochure, where you can find additional information on how the Defrost Sensor works and the installation process.
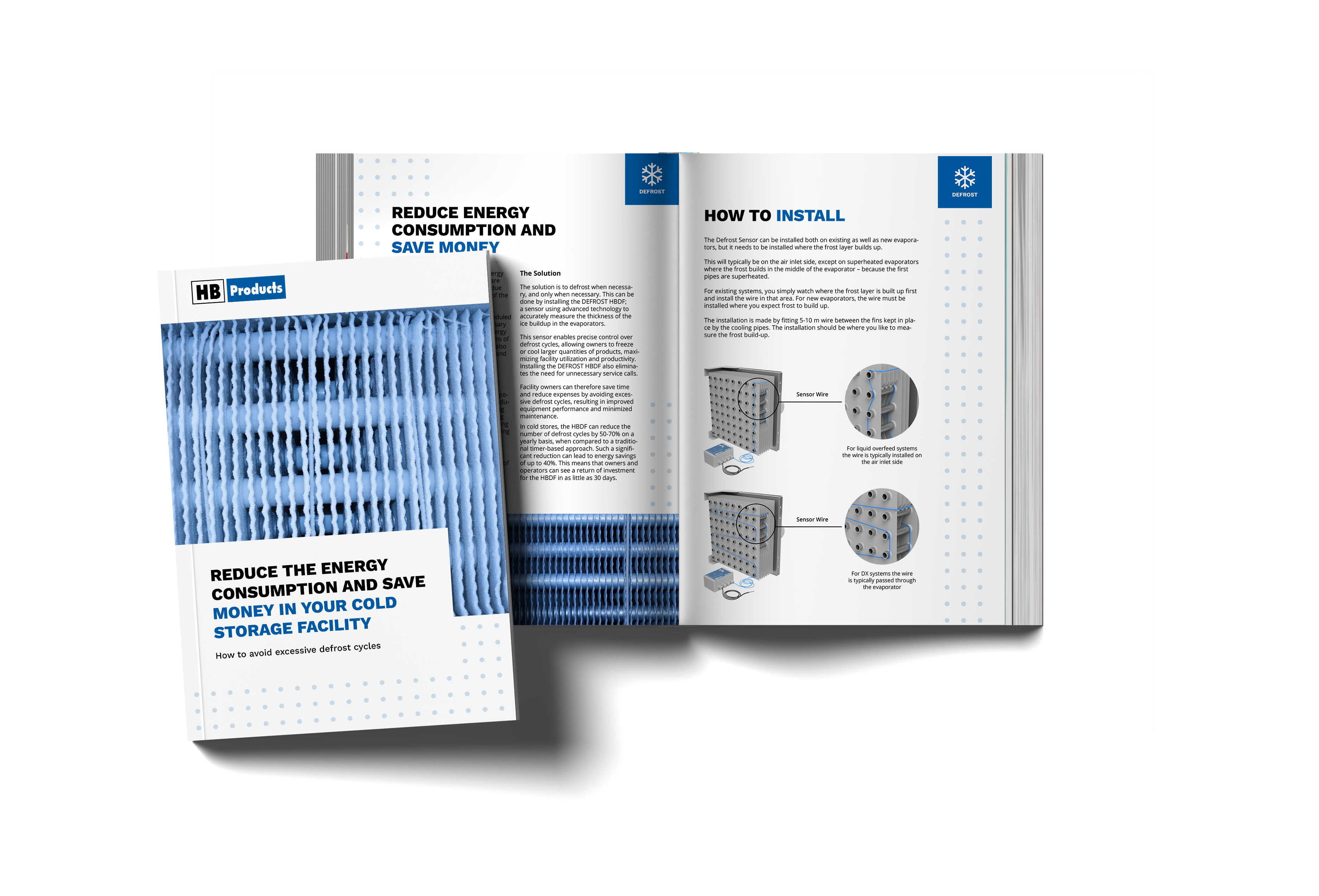
What Is Your Potential Savings by Optimizing Defrosting?
Our Defrost Sensors ensure automatic defrosting based on the capacitive measuring principle, thereby eliminating excessive defrost cycles.
You can calculate your potential savings with our calculator. It is based on the conservative estimation of a 50% reduction, while the heat calculation is based on the Danfoss Liquid Drain method.
Systems using hot gas with pressure control and systems using electrical heating or hot water will consume more energy.
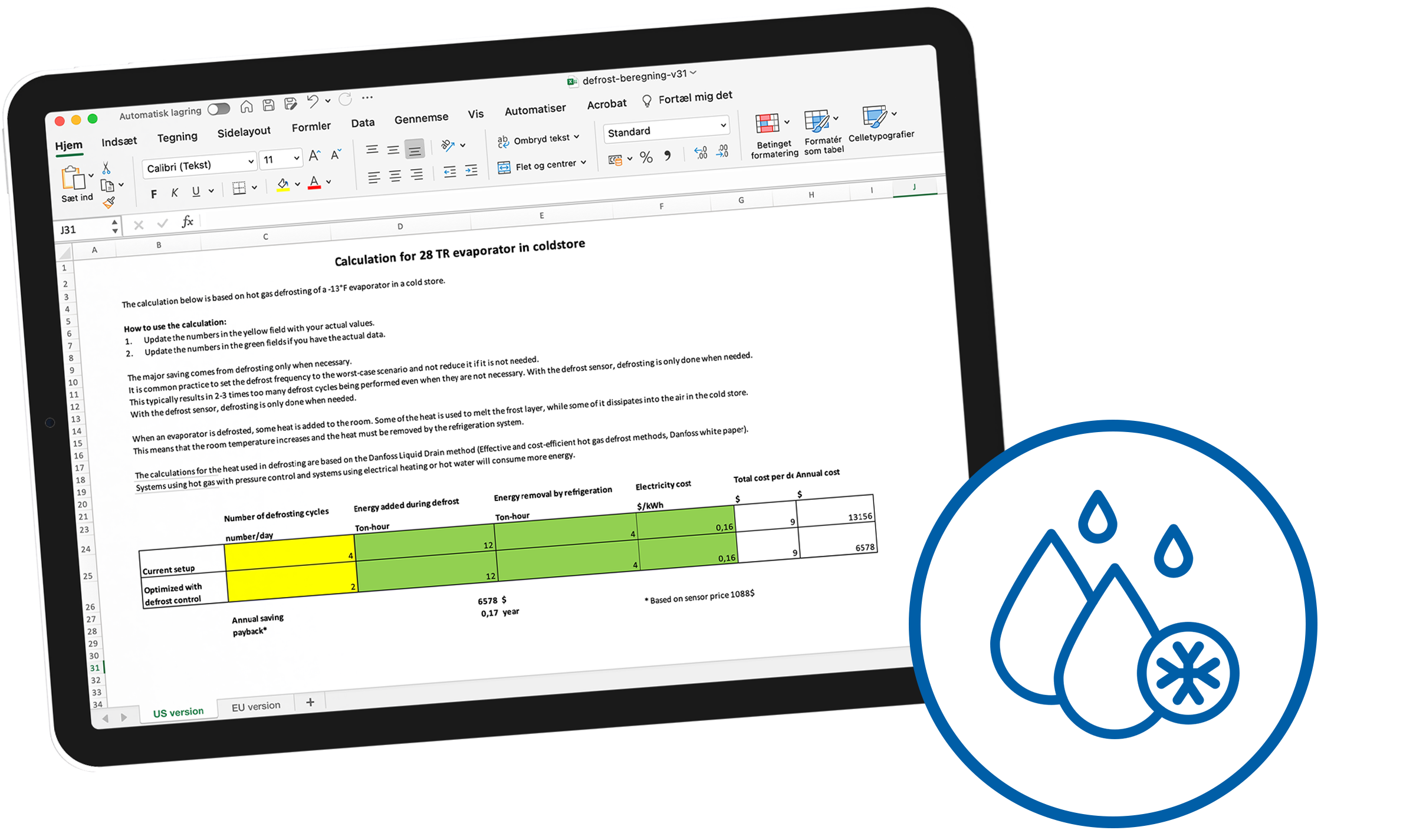
AB-Catering Eliminated Issues With Condensation and Continual Adjustments
For AB-Catering, their defrost cycles had caused serious issues for years, as they needed to adjust the cycles regularly, especially every time spring and fall rolled around.
In addition, they were having problems with condensation that dripped down on the conveyor belt and then froze to ice.
The solution to their problems was the Defrost Sensors from HB Products. Read the entire case study if you are curious about the solution and collaboration.
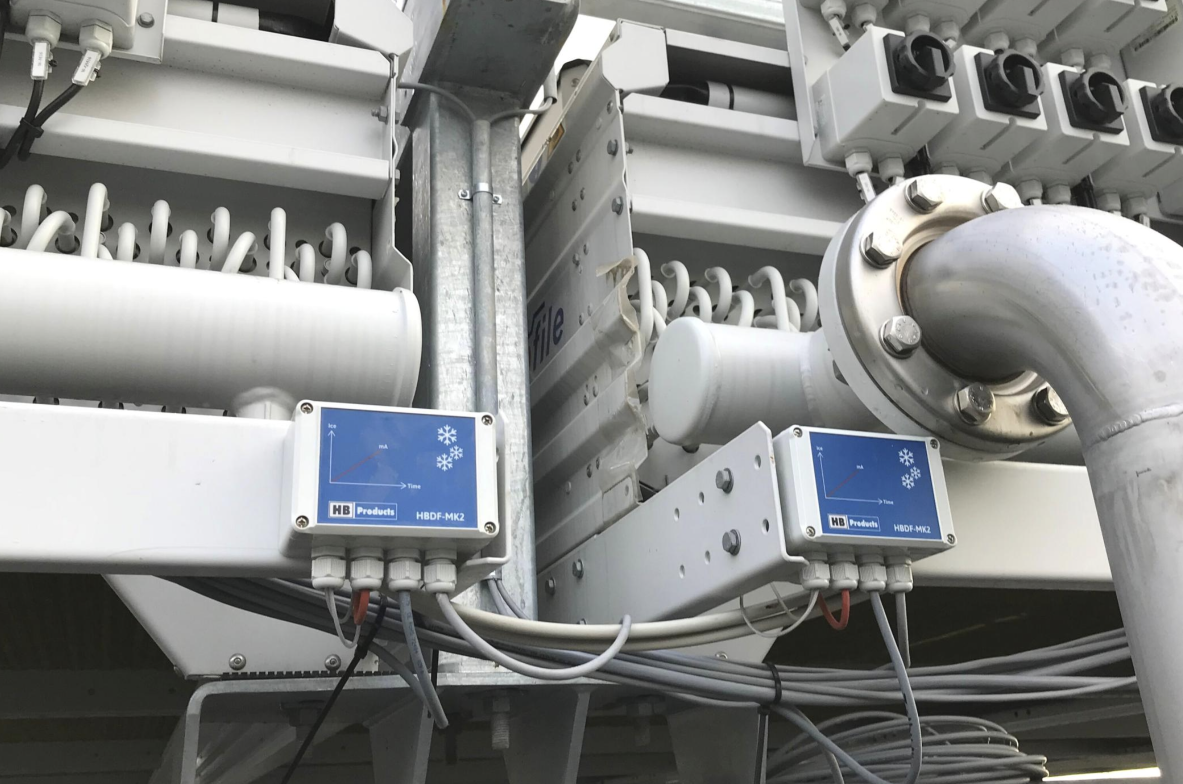
Store Ice During Off-Peak Hours with Our Ice Bank Sensor
Our Ice Bank Sensor is designed to optimize ice storage management in industrial and commercial refrigeration systems.
Using the capacitive measuring principle, the sensor accurately monitors ice build-up, enabling efficient ice storage during off-peak hours. This not only reduces energy consumption but also enhances system reliability by preventing excessive ice formation.
Watch the Ice Bank Sensor in action through the animation.
You Might Also Be Interested in Looking
at Our Other Products
Energy-Saving Vapor Quality Sensors Suitable for All Refrigerants
Our Vapor Quality Sensor is designed to measure the liquid content in the evaporator’s output and works in both liquid overfeed and DX systems. The Vapor Quality Sensor provides instant measurement and feedback to improve efficiency, ensure more consistent performance, and optimize energy-consumption. We have documented savings of up to 20% during full load and 50% during part load for a DX ammonia system.
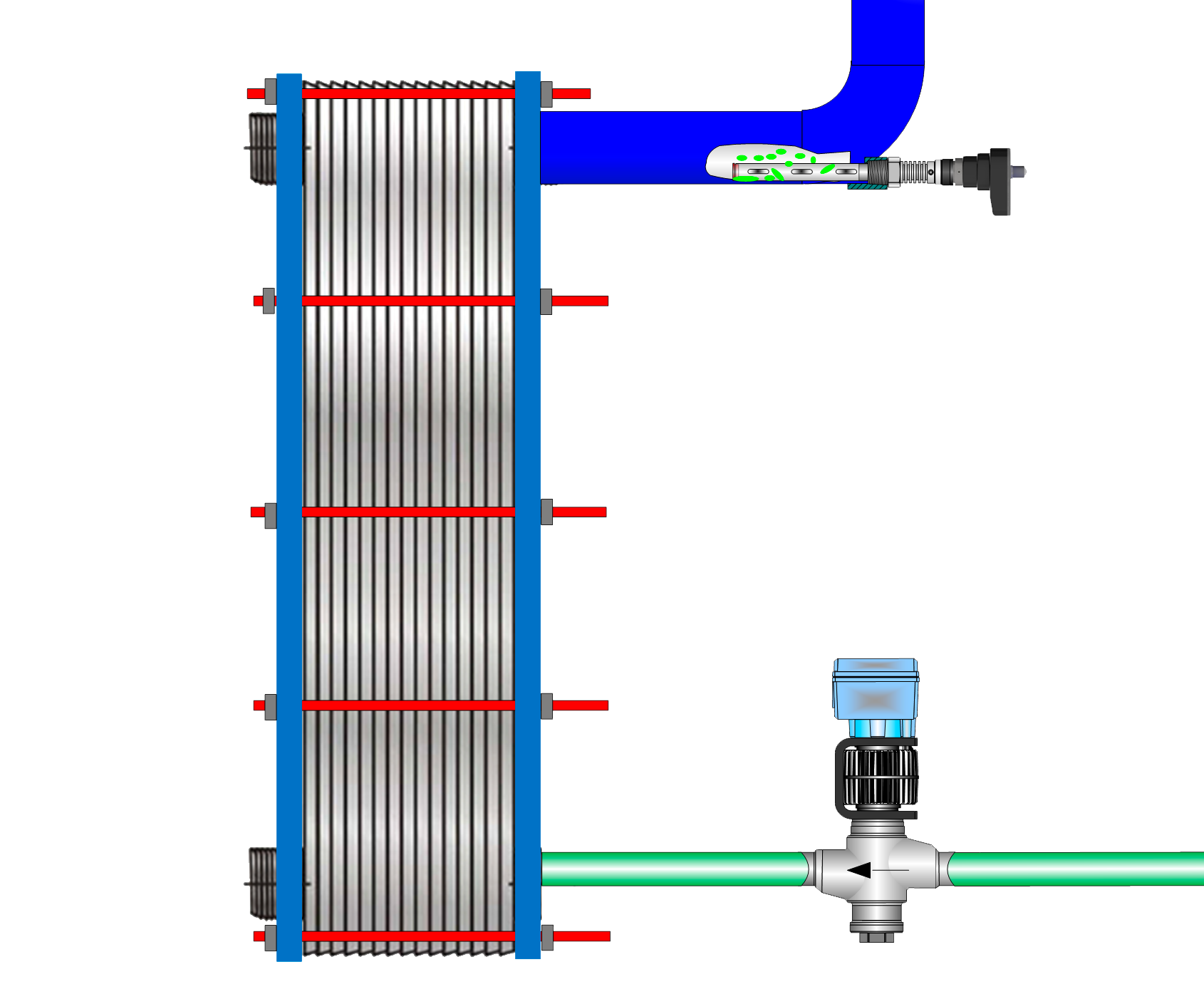
Control the Liquid Flow and Improve Operations With Our Vapor Quality Sensors
Energy-savings of at least 20%
Easy installation with split design
Suitable for all common liquids
Flexible installation on both horizontal and vertical pipes
Available pipe sizes ranging from 6 mm to 300 mm
Safeguard your compressor from liquid slugging
How to Achieve Better Control and Improve Energy-Efficiency With Vapor Quality Sensors
Are you interested in learning more about how our Vapor Quality Sensors function in liquid overfeed and DX systems? Download our brochure below, where you can find additional information, product specifications, and case studies.
ANZCO FOODS Saves Energy in Their Pumped System with Vapor Quality
Balancing cooling capacity and the lowest possible energy consumption is a challenge in many pumped refrigeration systems. This was also the case for ANZCO Foods.
To alleviate this problem, they installed our Vapor Quality Sensors into their ammonia tunnel freezer system, and despite a complex system design, the sensors were successfully installed.
“The installation of the HB Products vapor quality sensors made the project operate successfully at extremely low temperatures. We are still not sure how this project could have been installed without their use,”
Dennis Carswell, ANZCO FOODS
You can read more about the installation and operational design constraints in the full case study.
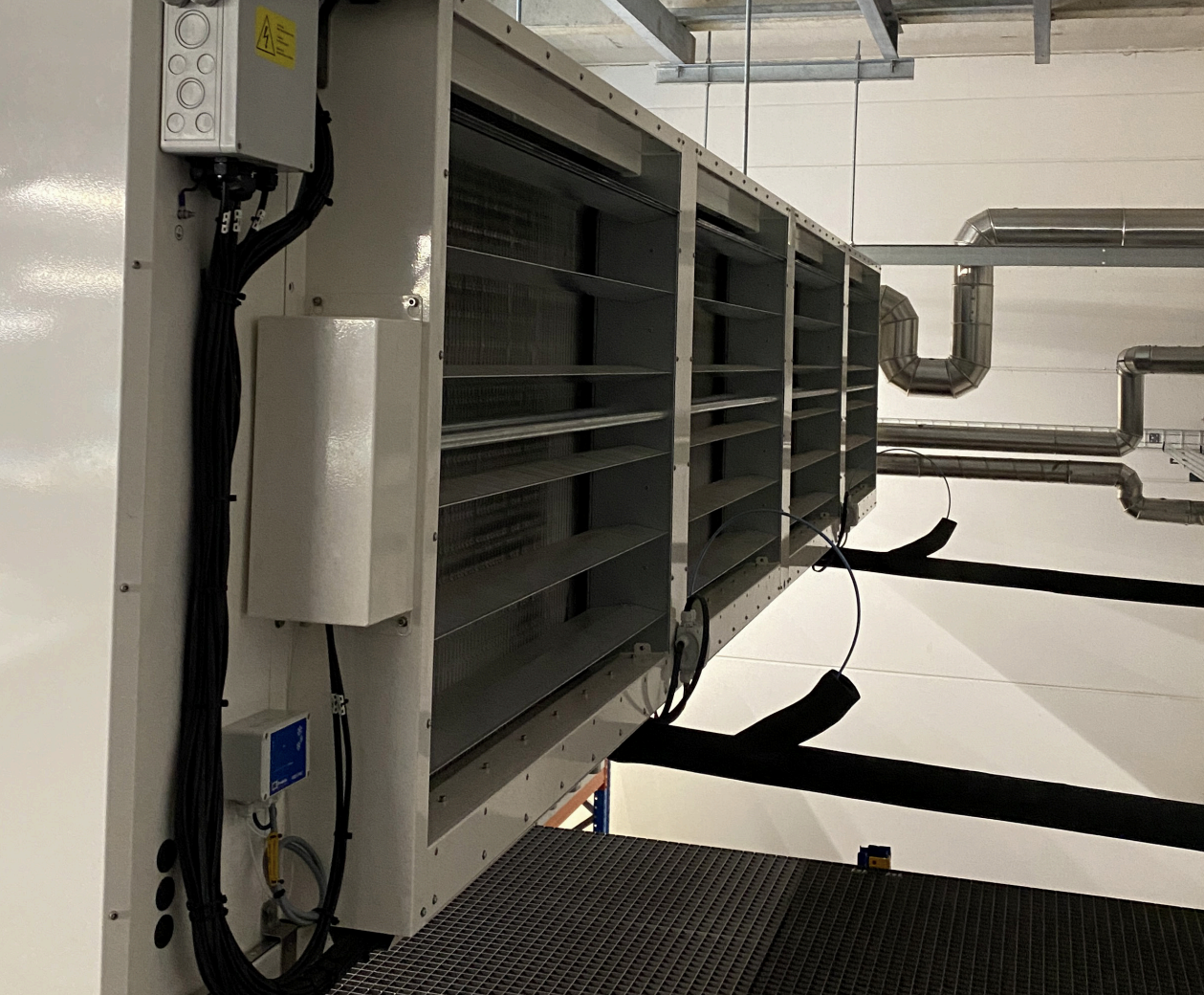
You Might Also Be Interested in Looking at Our Other Products
Control and Detect Liquid Levels With Our Wide Variety of Innovative Switches
With our Liquid Level Switches, you avoid the challenge of moving elements in mechanical switches, which get worn down and ultimately fail. All our Liquid Level Switches utilize capacitive measuring and are designed with a smart split design, ensuring easy maintenance and built to withstand challenging conditions like low and high temperatures, high pressures, and aggressive fluids.
Our Level Switches Are Designed for the Industry
Efficient and quick installation and diagnostics
Reliable performance in -60°C to 145°C (-76°F to 293°F)
Flexible power supply with both AC and DC power
Suitable for various liquids like ammonia, CO2, and butane
Easy plug-and-play configuration with HB Tool
See How Our Liquid Level Switches Work
Achieve a Simple Approach to Automatic Oil Return with Our Oil Management Program
Our product range includes sensors designed for measuring and transmitting oil levels.
The Oil Ejector combines an oil switch with an ejector, providing a simple and reliable solution for systems with ammonia or CO2, and eliminating the need for an expensive oil pot.
As it reuses some of the refrigerant in the system, it helps to optimize the refrigerant cycle and reduce the load on the compressor, which in turn reduces energy consumption.
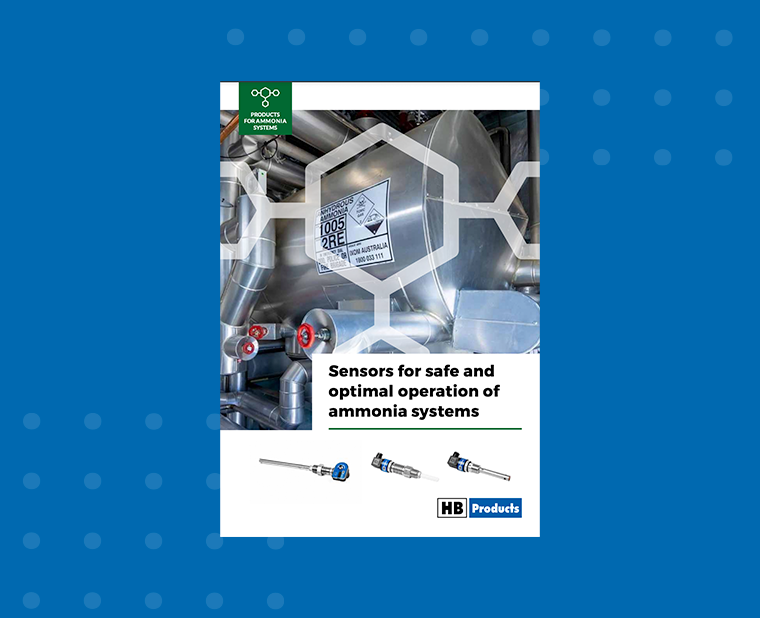
Our Sensors in ammonia systems

Our Switches in CO2 systems
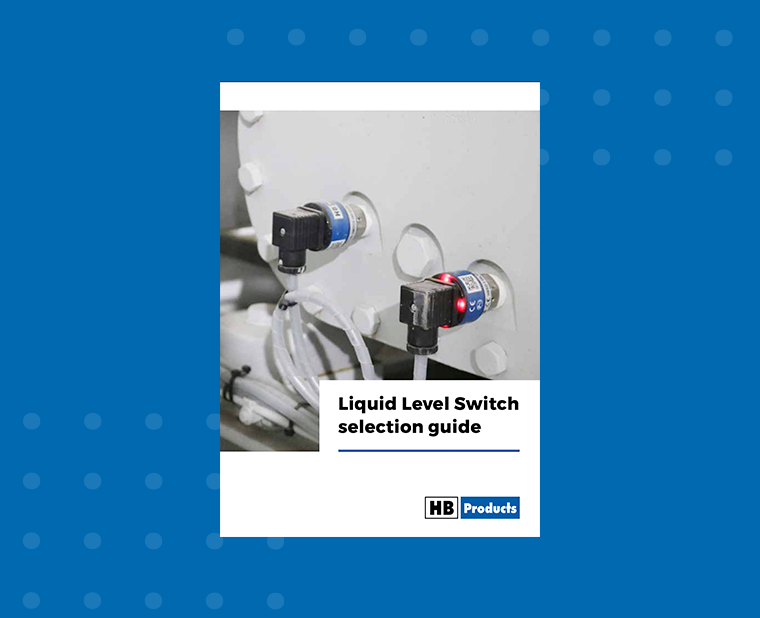
Liquid Level Switch Selection Guide
Mayekawa Nordic Found a Reliable and Robust Solution From HB Products
Mayekawa Nordic was in need of a new and durable oil and refrigerant management solution for their ammonia (NH3) chillers — they found it with our HBSR switch.
The switch is designed for industrial ammonia systems and is capable of withstanding pressures of up to 100 bar, while the split design proved to be a valuable feature.
“The separation between the mechanical and electrical part makes servicing easier. No need to drain the refrigerant charge to change a defective electronics component,”
Claus Ødegaard, Sales Manager at Mayekawa Nordic.
You can read the entire case study below.
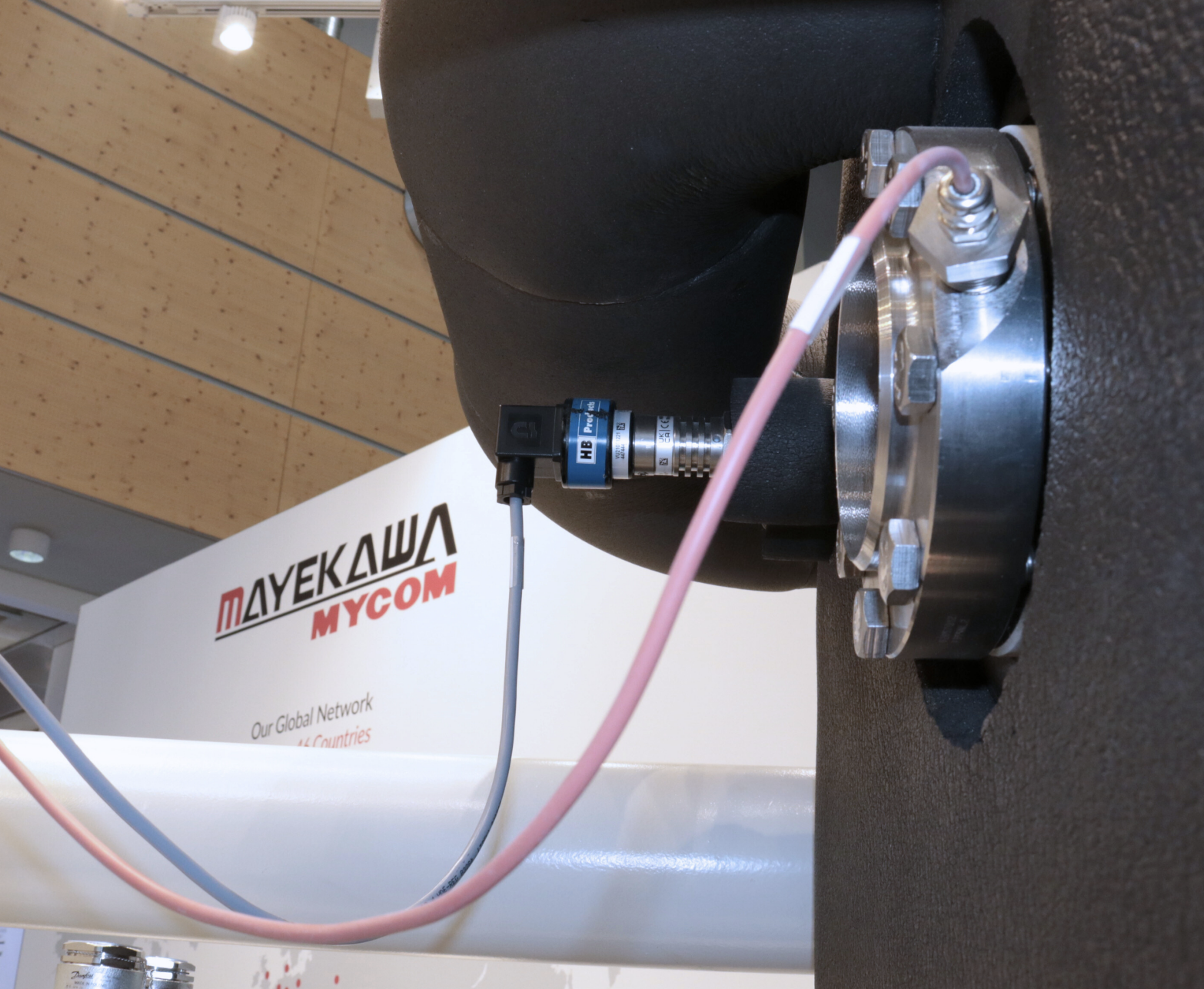
You Might Also Be Interested in Looking at Our Other Products
Precise Liquid Level Sensors for Both Natural and Synthetic Refrigerants
Are you looking to ensure a high-quality solution for every type of environment? Take a closer look at our Liquid Level Sensors. With a smart split design, our Liquid Level Sensors provide a durable, easily maintained, and cost-effective solution for accurate monitoring.
Our Level Sensors Are Designed for the Industry
Efficient and quick installation and diagnostics
Reliable performance in -60°C to 80°C (-76°F to 176°F)
Adjustable length of the mechanical part
Suitable for various liquids like ammonia, CO2, and butane
Easy plug-and-play configuration with HB Tool
See How Our Liquid Level Sensors Work
Achieve a Simple Approach to Automatic Oil Return With Our Oil Management Program
Our product range includes sensors designed for measuring and transmitting oil levels.
The Oil Ejector combines an oil switch with an ejector, providing a simple and reliable solution for systems with ammonia or CO2, and eliminating the need for an expensive oil pot.
As it reuses some of the refrigerant in the system, it helps to optimize the refrigerant cycle and reduce the load on the compressor, which in turn reduces energy consumption.
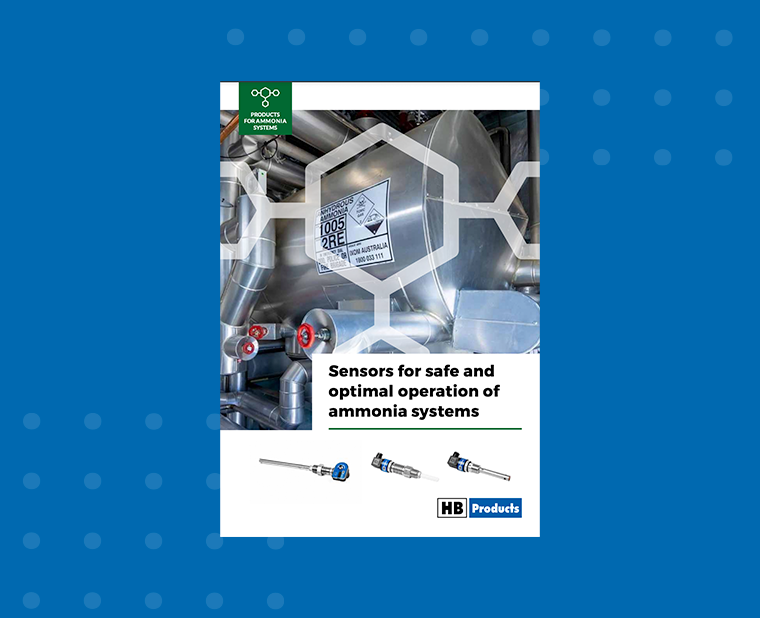
Our Sensors in ammonia systems
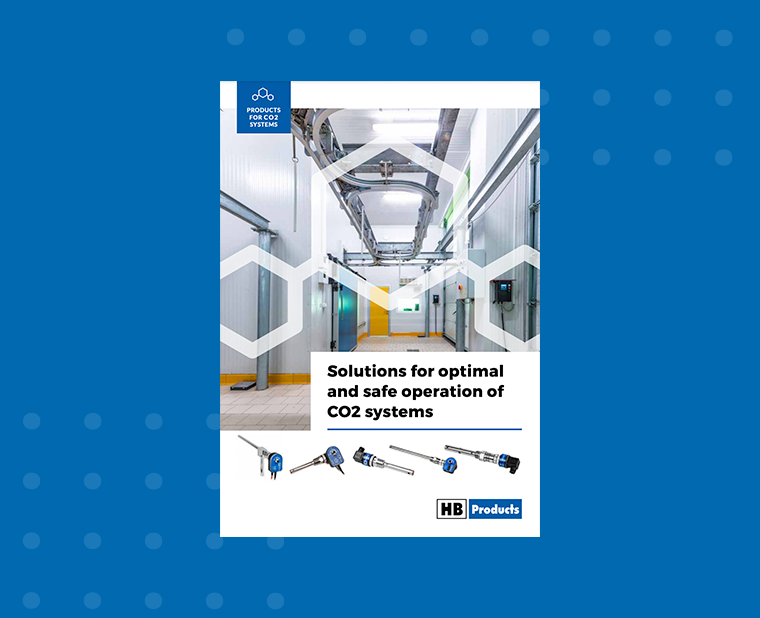
Our Sensors in CO2 systems
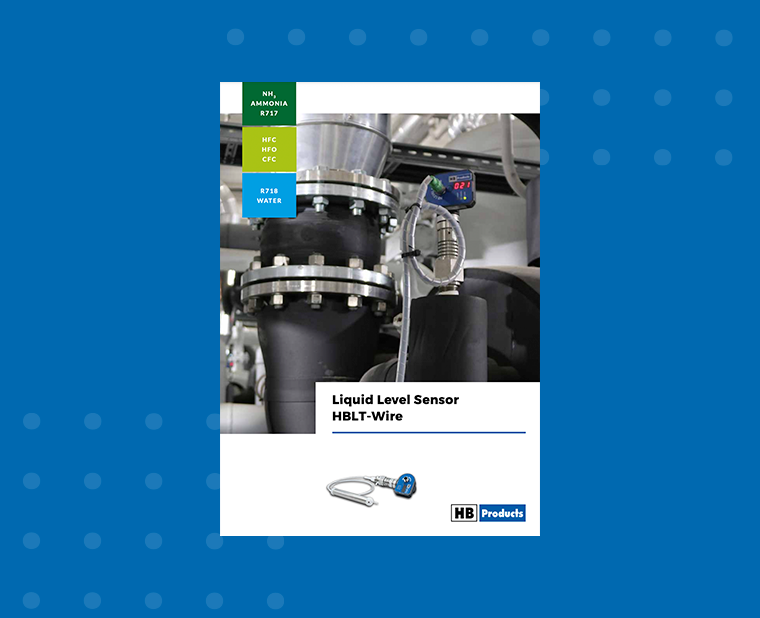
Liquid Level Sensor HBLT-Wire
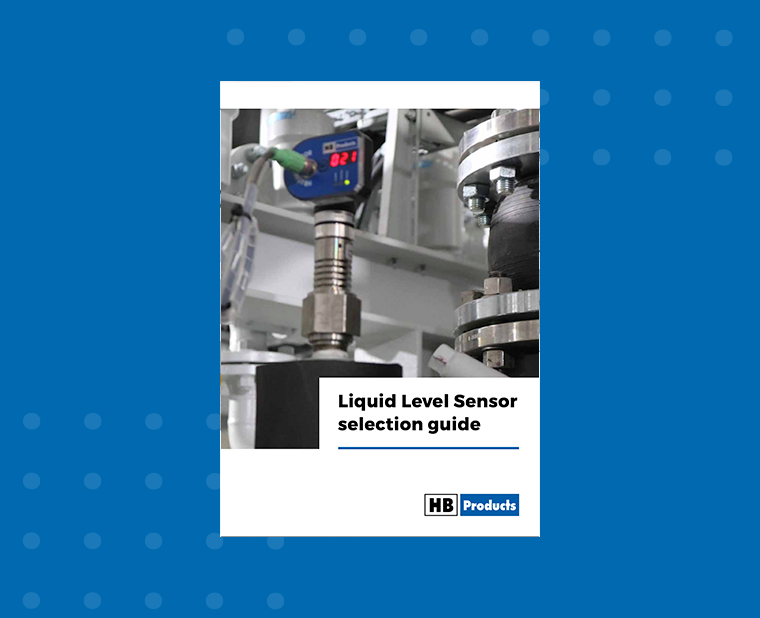
Liquid Level Sensor Selection Guide
Efficient Installation and a Durable Sensor for Exodraft Energy With HB Products
Exodraft Energy was in need of a highly durable Liquid Level Sensor for its ammonia containers. It was paramount that the sensors were capable of handling both cold and warm temperatures up to 70°C (158°F) without becoming unreliable.
The choice fell on our HB Products HBLT-A3 Liquid Level Sensor, which was integrated into the operation without incident and with great results.
You can read the entire case story and learn more about the specifications of the HBLT-A3 Liquid Level Sensor below.
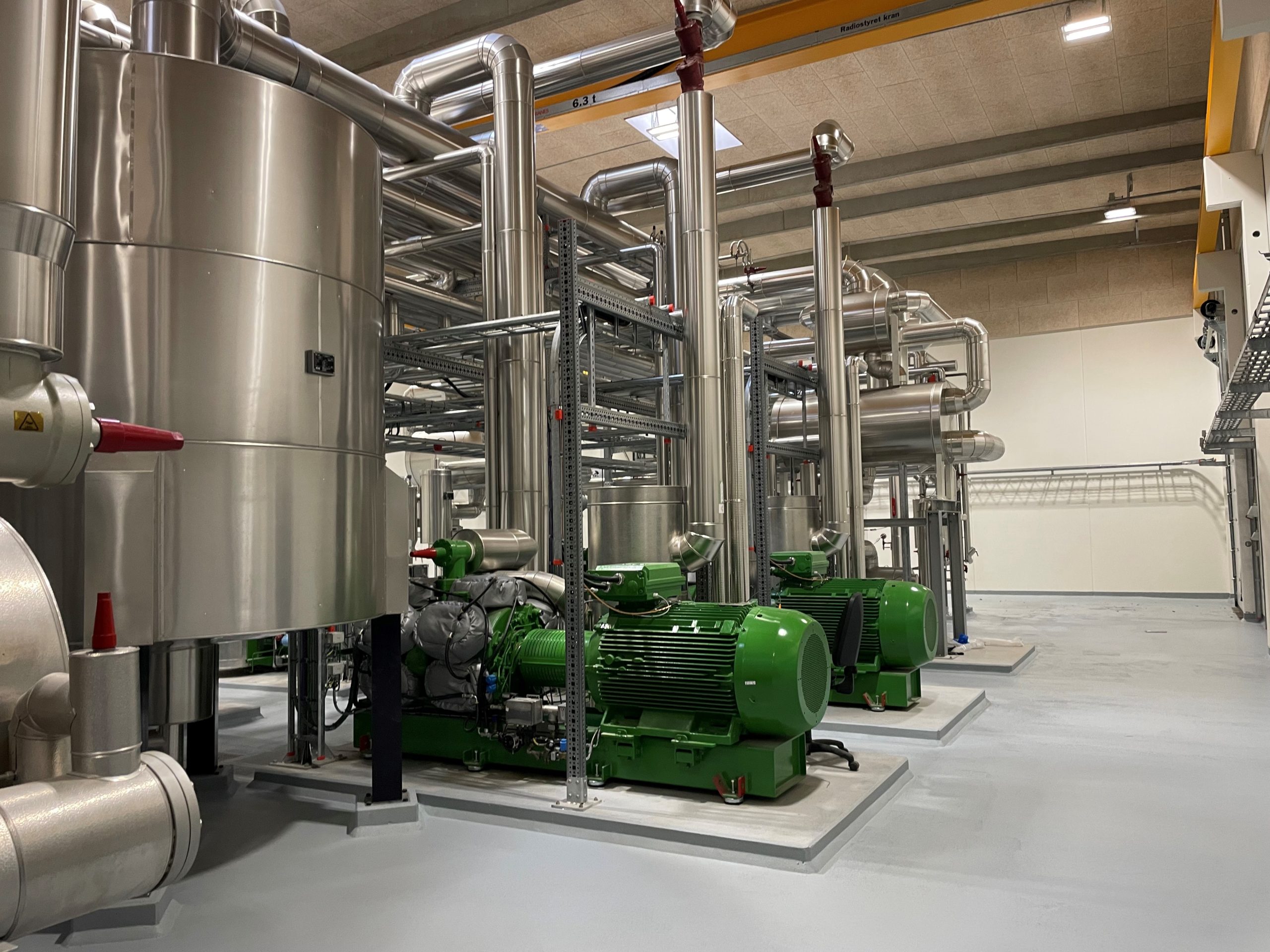